车床尾座体机械加工工艺规程与夹具设计
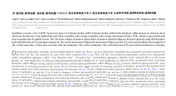
1.无需注册登录,支付后按照提示操作即可获取该资料.
2.资料以网页介绍的为准,下载后不会有水印.资料仅供学习参考之用.
密 惠 保
摘要
本次设计的课题是车床尾座体规程及粗、精铣355mmX150mm上平面专用。车床尾座体位于车床的末端,主要作用是加工长轴时,用于防止因装夹误差发生径向跳动。因此,车床尾座体的加工质量将直接影响加工工件的质量。本次设计旨在保证质量提高加工效率,由此首先我们对其进行工艺性分析,确定毛坯类型为砂型铸造和毛坯尺寸。制定合理的工艺路线,采用万能机床配以专用,并尽量使工序集中起来提高生产率。为提高劳动生产率,保证加工质量,降低劳动强度,需设计专用夹具,为此选择了第三道工序——粗、精铣355mmX150mm上平面铣床夹具,以满足加工过程的需要。
关键词:车床尾座体、工艺规程、夹具
零件的作用:
题目所给定的零件是车床尾座体,它位于车床的末端,主要作用是当加工长轴时,用于顶紧工件防止因装夹误差发生径向跳动.零件的顶部有一个φ100H7mm的孔,用于安装一个顶尖在尾座体末端,用一个手轮夹操作顶尖的进退,尾座体顶部有一个φ30H7mm的孔,并有M8的配钻螺纹孔。用于锁紧顶尖;另外,顶部还有一个φ10mm的梯形孔,作用是加润滑油,使顶尖能移动自如;在套筒的旁边,还有一个φ50mm的孔,用于使顶尖偏心,调整加工时的不同椎度,在尾座体底面有一个矩形槽,用于能通过手柄使尾座体能左右移动。 [来源:http://www.think58.com]
工艺性分析:
车床尾座体共有两组加工表面,它们相互间有一定的位置要求,现分析如下:
A、以φ100H7mm为中心的加工表面,这一组加工表面包括:
a、φ100H7mm孔及其倒角:公差等级为IT7,表面粗糙度为Ra0.8μm,并有圆柱度要求,公差为0.012,需粗镗、半精镗、精镗、。
b、φ120H8mm的孔:公差等级为IT8,表面粗糙度为Ra1.6μm,需粗镗、半精镗、精镗。
c、φ30H7mm孔:公差等级为IT7,表面粗糙度为Ra1.6μm,并有位置度要求为0.08,需钻,扩,粗铰,精铰。
d、φ10H7mm孔:公差等级为IT7,表面粗糙度为Ra1.6μm,需粗铰-精铰。
e、φ6mm孔:未注公差,表面粗糙度为Ra12.5μm,只需钻就可以了。
f、φ50H7mm孔:公差等级为IT7,表面粗糙度为Ra1.6μm,并有位置度要求,位置度公差为0.07,需钻-粗铰-精铰。
g、φ77mm孔:没公差要求,表面粗糙度为Ra6.3μm,锪。
h、4-M12深20mm孔:未注公差及表面粗糙度,需钻-攻。
i、两个端面:后端面有垂直度要求,表面粗糙度为Ra3.2μm,需粗铣-精铣。
j、顶面:未注公差等级,表面粗糙度为Ra1.6μm,需粗铣-精铣。
B、以底面为中心的加工表面。这组加工表面包括:
a、底面:未注公差等级,表面粗糙度Ra1.6μm,平面度要求为0.04,需粗铣-精铣-刮研。
b、底面四周:未注公差等级,表面粗糙度Ra3.2μm,需粗铣-精铣。
c、底面的两孔2-φ33mm:未注公差等级,表面粗糙度Ra12.5μm,需钻即可。
d、2-φ61mm及倒角:未注公差等级,表面粗糙度Ra12.5μm、Ra6.3μm,锪。
e、φ17mm孔:未注公差等级,Ra12.5μm,钻。
f、螺纹M20×45mm:未注公差等级,在φ17mm基础上扩孔至φ17.5mm,深50mm,再攻M20×45mm。
h、φ17.5mm孔:未注公差等级,表面粗糙度Ra12.5μm,需钻即可。
i、φ26mm,φ20mm螺纹:表面粗糙度Ra12.5μm,需扩孔至φ20mm,再攻螺纹,深20mm。
j、钻φ17.5mm孔,扩孔至φ26mm,深20mm,再将剩余部分攻φ20mm的螺纹。
k、62mm×24mm的槽:未注公差等级,表面粗糙度为Ra12.5μm,其中G面Ra1.6μm,需刮研。
[资料来源:http://THINK58.com]
l、3mm×2mm的退刀槽:未注公差等级,表面粗糙度为Ra12.5μm,粗刨即可。
这两组加工表面之间有着一定的位置要求,主要是:
φ30H7mm孔中心线与φ100H7mm孔中心线的位置度公差为0.08;
端面F与φ100H7mm孔中心线的垂直度公差等级0.02;
G端与φ100H7mm孔中心线的垂直度公差等级0.03,与底面的垂直度公差为0.08;
φ100H7mm孔中心线与底面的平行度公差为0.12;
φ50H7mm孔中心线与φ100H7mm孔中心线的位置度公差为0.07;
φ100H7mm孔的圆柱度公差为0.012;
底面的平面度公差为0.04。
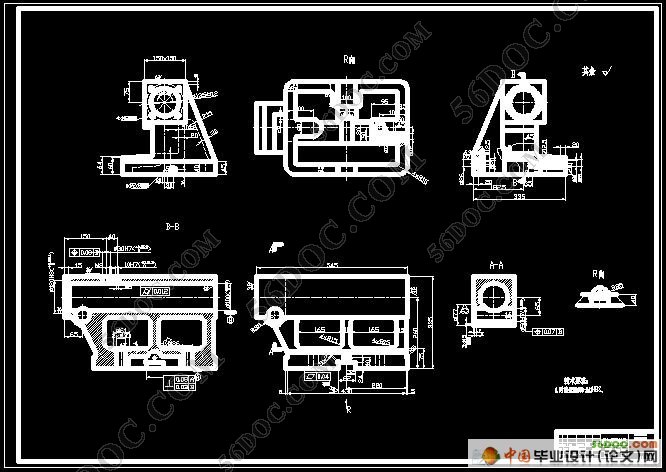
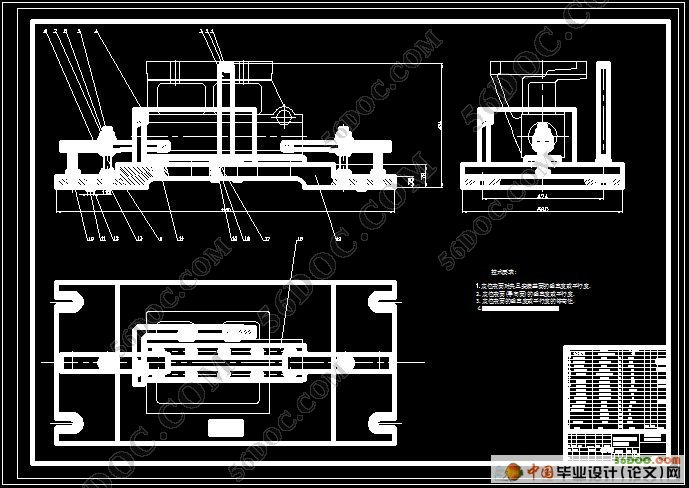
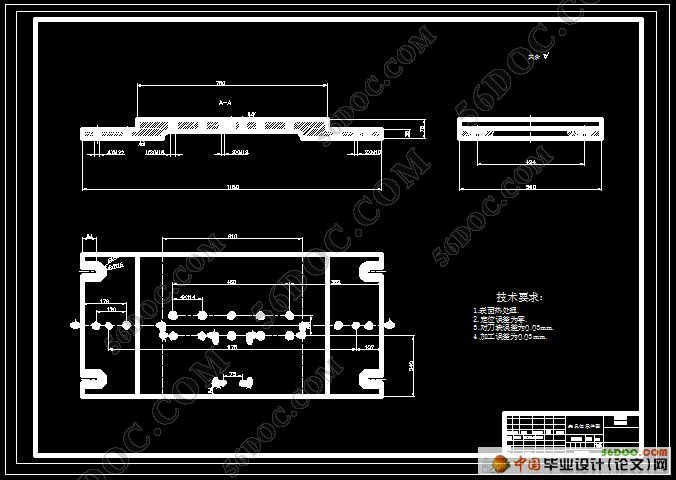
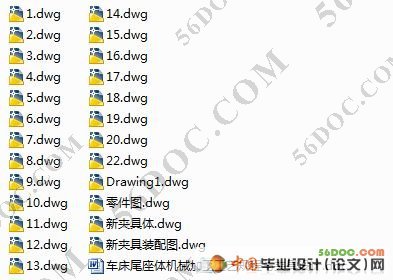
目 录 11000字
1.前言……………………………………………………3 [版权所有:http://think58.com]
2.零件的分析……………………………………………4
3.确定毛坯………………………………………………5
4.制定工艺路线…………………………………………7
5.确定切削用量及基本工时……………………………8
6.专用夹具设计…………………………………………30
7.总结……………………………………………………32
8.参考文献………………………………………………33 [资料来源:http://think58.com]
9.附录……………………………………………………34
[资料来源:http://think58.com]
上一篇:加工涡轮盘榫槽的卧式拉床夹具设计