支承座三工序复合冲压模具设计(含CAD零件图装配图)
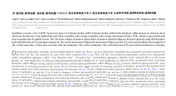
1.无需注册登录,支付后按照提示操作即可获取该资料.
2.资料以网页介绍的为准,下载后不会有水印.资料仅供学习参考之用.
密 惠 保
支承座三工序复合冲压模具设计(含CAD零件图装配图)(任务书,开题报告,外文翻译,论文说明书10000字,CAD图6张)
摘 要
本文主要对支承座三工序复合冲压模具的结构、工作原理、主要工作部件的设计和参数计算进行了部分介绍。通过采用新型的三工序复合冲压模具,可以使工件毛坯的落料、冲孔和弯曲三个工序在一个工步中成形。该模具的特点是生产效率高,工艺质量好。所得结果对于支承座进行大批量生产具有重要的指导意义。
本次设计共分为三个阶段完成。第一,首先参考实践成果,确定主要的冲裁工艺方案与结构。第二,对相关尺寸进行计算,同时确定模具草图。第三,利用CAD绘制模具总装图以及零件图,同时完成说明书。
关键词:复合模具;冲压;支承座
Abstract
This article has described the structure,work principle,the design methods of the key parts such as the punch,concave die,oblique plane and the design calculation of main parameters. There-process composite die can carry out cutting and punching and bending in one process. The goodness of this technology is that productivity is high and part quality is generous.The results have important guiding significance for the mass production of the structure.
[资料来源:www.THINK58.com]
The whole mold design was divided into three stages. Firstly, the punching process and structure were determined carefully on both theoretical and practical basis. Secondly, the mold dimensions were calculated and the mold structure drawing was initially designed. Thirdly, the CAD software was adopted to draw the mold assembly and part drawings, and then the research report was written.
Key Words:composite;stamping;cradle
工作原理
本次设计出来的模具的工作原理是:当模具处于模架最上端将要开始启动处时,将坯料放在成形凸模和落料凹模之间存在的空隙上,同时利用侧板和定位销的定位作用来进行位置确定。当压力机开始向下压,压床滑块向下移动,推动上模座向下移动。首先,在弹簧的向下压力作用下,坯料被压料版紧紧压在成形凸模上,此时固定斜楔向下移动,并与凹模配合将坯料的落料工序完成,于此同时,冲孔凸模向下移动,在工件上完成Φ20mm小孔的冲孔工序;接着,压床滑块继续推动上模座向下移动,毛坯在固定斜楔的作用下开始进行U形的弯曲工序;同时活动斜楔在固定斜楔推动里下向模具中心压紧,使模具向内部弯曲,将两个边向内折弯。最后上模座到达极限最下点并开始随滑块向上运动,固定斜楔首先退出落料凹模,冲孔凸模也和成形凸模开始分离,弹簧则回复推动活动斜楔向模具外侧移动。等到行程结束后,便可直接将已完成所有工序的工件中取出。
由零件图可知,该工件材料为1Cr18Ni9Ti钢板。主要用于制作耐酸容器及设备,抗磁仪表、医疗器械,具有较好耐晶间腐蚀性。该钢板的抗拉强度为
屈服强度为 ,同时具有优良的力学性能,可以用于各类冷冲压工件。
3.2冲裁件的结构工艺性
3.2.1冲裁件的形状
冲裁件的外形形状相对简单,结构左右对称,便于充分利用材料,减少了材料的浪费。
3.2.2冲裁件的尺寸精度及表面粗糙度
采用普通冲裁的精度,可以通过查表得外形与内孔尺寸公差为0.50。并要求冲裁件剪断面表面粗糙度Ra6.3um。
3.4冲压工艺方案的确定
该工件需要进行落料工序,冲孔工序,弯曲工序。有以下几种工艺方案:
方案一:全部采用单工序模,首先进行落料工序,再进行冲孔工序,最后进行弯曲工序。
方案二:复合模和单工序模互相结合,先进行落料冲孔工序,再进行弯曲工序;
方案三:使用单一复合模,在一套模具中完成三道工序。
方案一的模具结构简单,但是三道工序只能分开进行加工,需要设计三套不同的模具来进行生产,生产效率较低,生产周期较长,不太适合实际的生产,加工不能达到预期的目的。方案二需要两套模具,但是第二套模具无法保证弯曲的精度,生产效率虽然比方案一高,但还是较低。方案三仅需要一套模具,相对前两套方案,生产效率较高,便于保证冲压件的形状精度和尺寸精度,且由于工件的几何形状简单,左右对称,便于模具制造。最终决定采用方案三比较好。
[资料来源:www.THINK58.com]
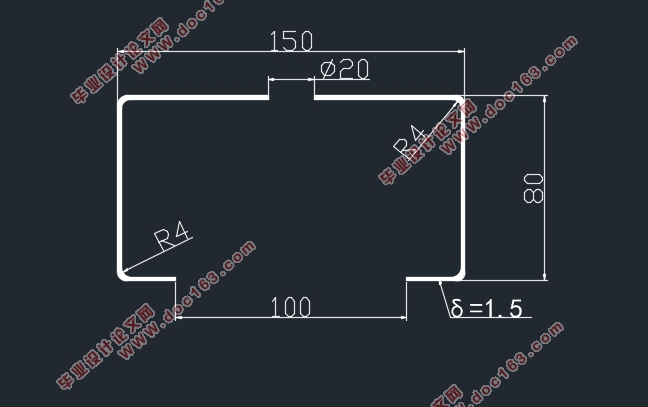
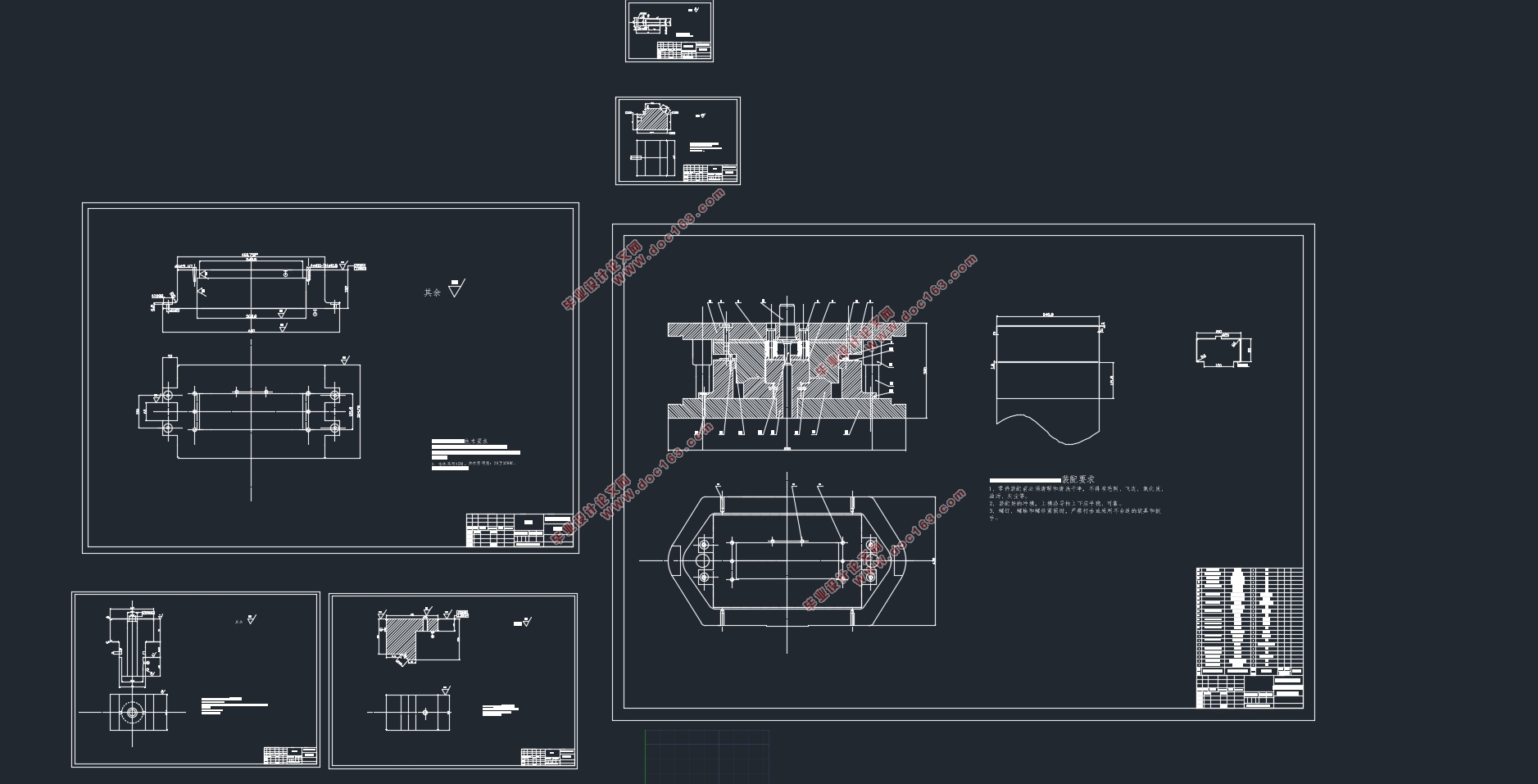
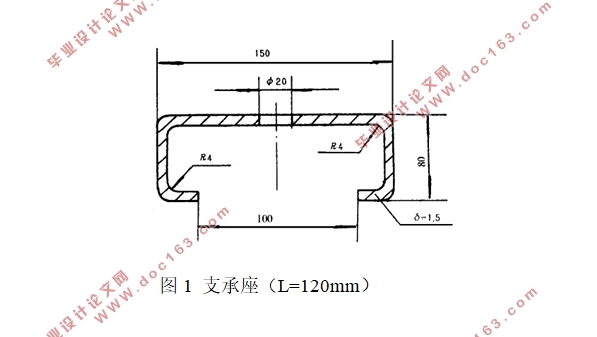
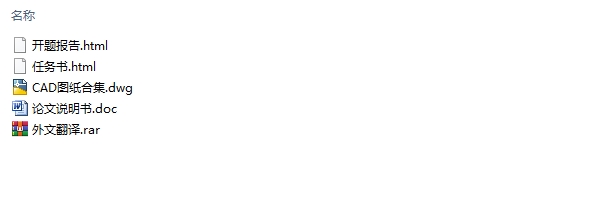
目 录
第1章 绪论 1
[资料来源:http://www.THINK58.com]
1.1 引言 1
1.2 任务分析 2
第2章 模具结构与工作原理 4
2.1模具结构 4
2.2 工作原理 4
第3章 主要设计计算 5
3.1材料分析 5
3.2冲裁件的结构工艺性 5
3.2.1冲裁件的形状 5
3.2.2冲裁件的尺寸精度及表面粗糙度 5
3.4冲压工艺方案的确定 5
3.5 毛坯尺寸的确定 5
3.6冲裁件的排样设计 6
3.7条料宽度和导尺间距离的计算 6
3.8材料利用率的计算 7
3.9冲压力的计算 8
3.9.1冲裁力的计算 8
3.9.2推件力的计算 8
3.9.3弯曲力的计算 8
3.9.4弯曲压料力的计算 9
3.9.5弯曲回弹的计算 9
3.10压力中心的计算 10
3.11压力机的选择与比较 10
3.12凹模周界的确定 12
3.13模架的选择 13
3.13.1上模座的选择 13
3.13.2下模座的选择 14
3.14模架导向装置的选择 14
3.14.1导柱的选择 14
3.14.2导套的选择 15
3.15模具连接与固定零件 15
3.15.1模柄 15
3.15.2垫板 15
3.15.3固定板 15
3.15.4档料销及定位销 15
3.15.5螺钉 16
3.15.6推杆 16
3.16弹性元件的确定 16
第4章 主要工作零件设计 17
4.1冲孔凸模 17
4.1.1承压应力校核 17
4.1.2失稳弯曲应力校核 18
4.2成形凸模 18
4.3落料凹模 19
4.3.1刃口尺寸计算 19
4.4斜楔 19
4.3.1固定斜楔 19
4.3.2活动斜楔 21
4.3.3斜楔行程计算 22
参考文献 24
致 谢 25
[资料来源:http://www.THINK58.com]
上一篇:某筒形件拉深模具的三维设计及有限元分析(含CAD装配图,CATIA三维图)
下一篇:90°弯头注塑成型工艺分析与设计(含CAD零件图装配图)